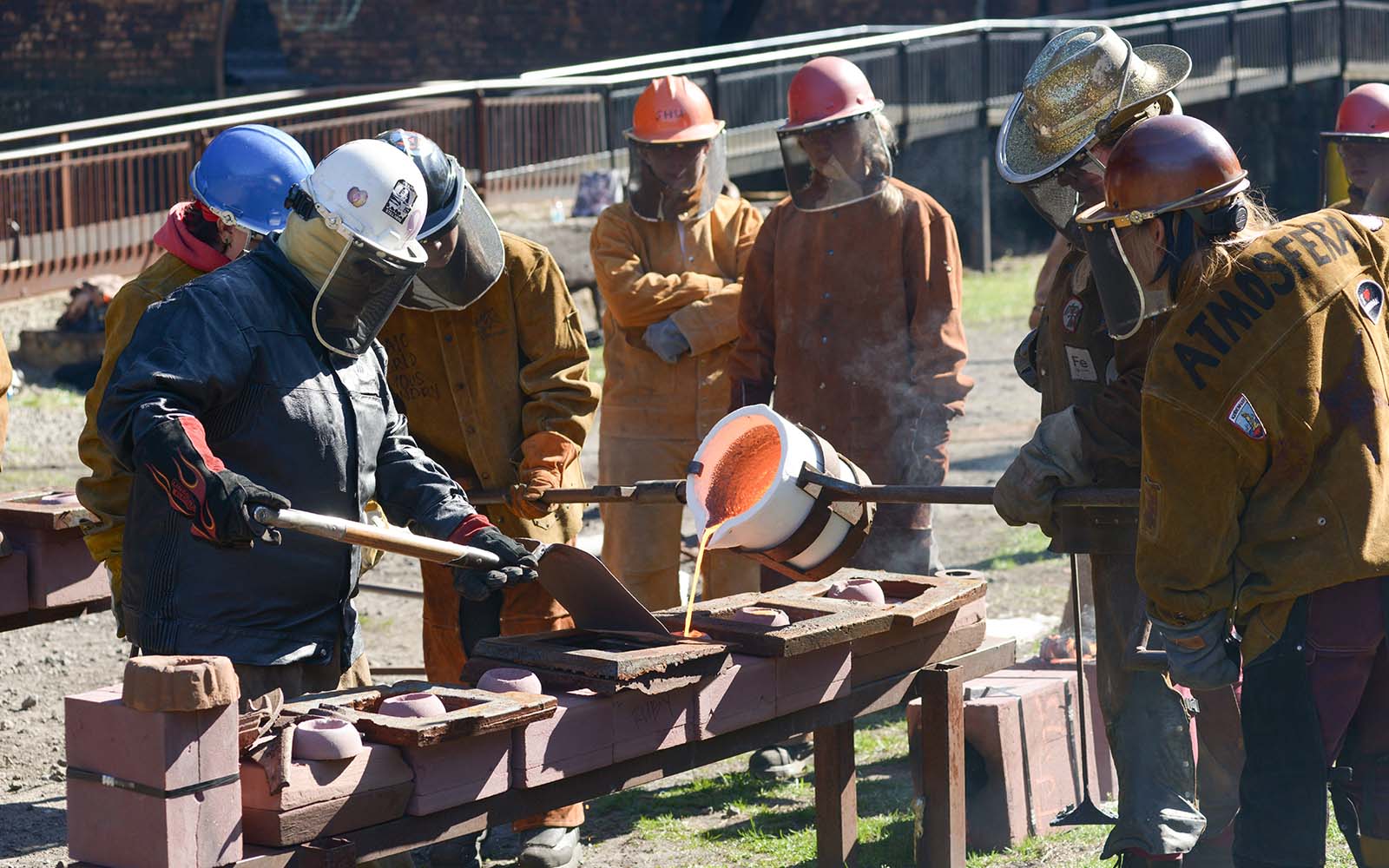
Coral Penelope Lambert works with five students to pour iron from a smaller ladle while two more students observe during last Saturday’s inaugural Intercollegiate Iron Pour at the Carrie Blast Furnaces.
The Inaugural Intercollegiate Iron Pour
By Lynne Squilla, Contributing Writer
With Carrie’s majestic Blast Furnace #6 towering behind them, thirty college students and mentoring artists gathered on a brisk March weekend to pour their own iron creations and forge ongoing connections among the metal arts community.
Rivers of Steel’s first Intercollegiate Iron Pour drew students from Carnegie Mellon University, Alfred University in New York, Shepherd University in West Virginia, SUNY Cortland in New York, Seton Hill Greensburg, Chicago Art Institute, and NYU, who were joined by seasoned Rivers of Steel staff and alumni from past iron-pouring events hosted at the National Historic Landmark. Suited up in protective leather aprons and chaps, spats, boots, gloves, masks, and safety glasses, the students put their faces near the fire for a one-of-a-kind encounter with iron casting, sharing their passion for working with this challenging but captivating medium.
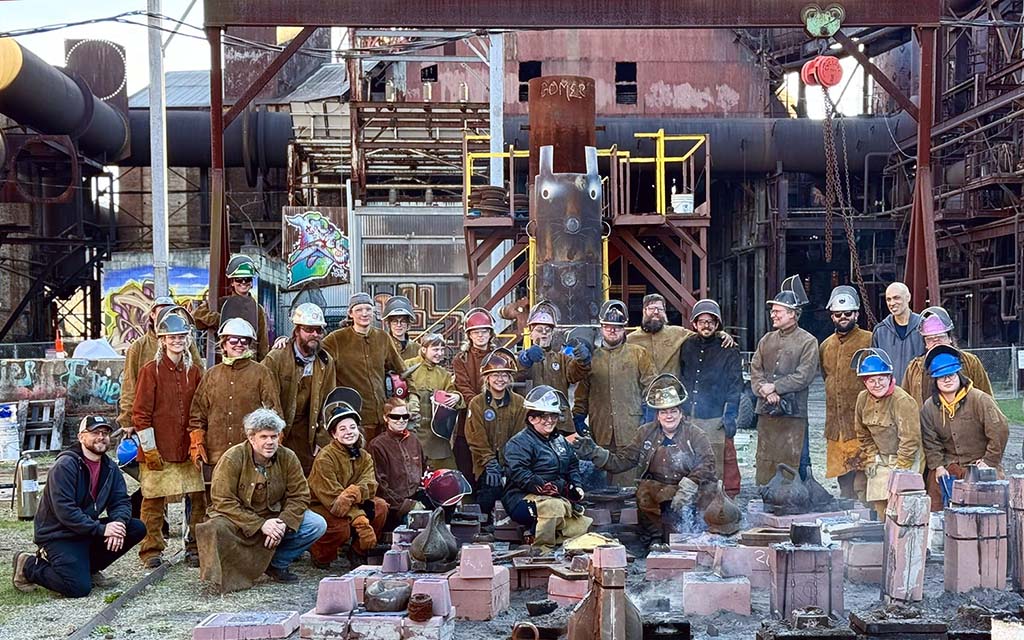
The crew of the first Intercollegiate Iron Pour.
“It’s just brilliant,” said Alfred University’s Coral Penelope Lambert, professor of sculpture dimensional studies and director of the National Casting Center Foundry. “This place is a sacred site, almost like Stonehenge. The grounds we walked on have this spirit of the industrial past, and that is a really rich thing for artists.” Lambert has been coming to Carrie since 2017, and her own work, called Gushers, was cast on site and now permanently graces the Iron Garden on the eastern side of the landmark site. For this pilot intercollegiate pour, she brought one undergrad and one graduate student from Alfred’s School of Art and Design, Sculpture Dimensional Studies Division, plus two Alfred alumni.
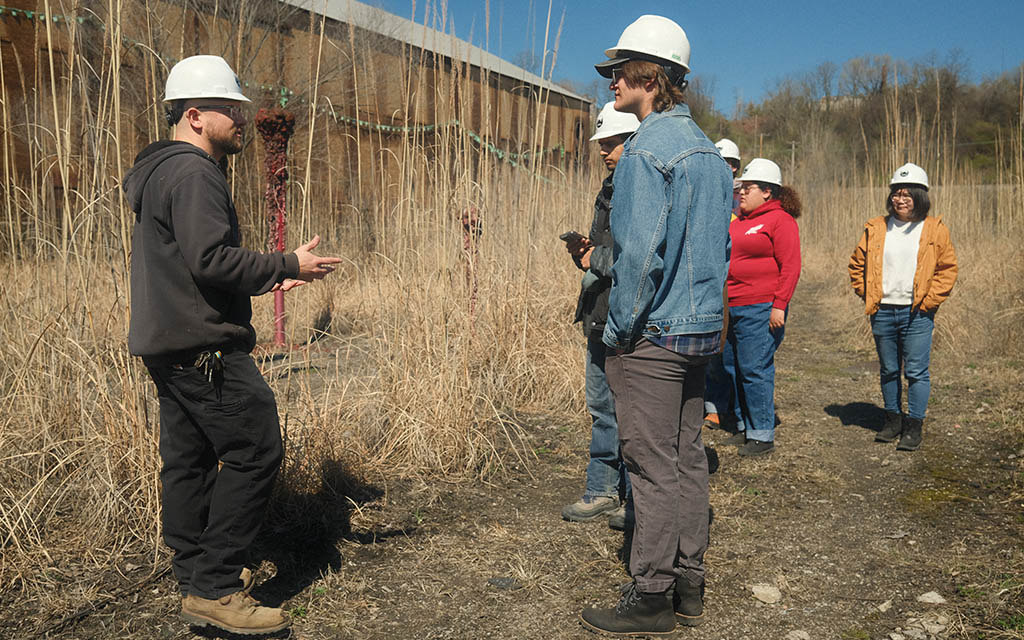
Chris McGinnis, Rivers of Steel’s director of arts, leads students through the Iron Garden. Coral Lambert’s sculpture is visible to the right of Chris.
“The ‘big sell’ here is you’re going to meet people who will become part of your network after college. It shows what can happen outside of academia and in the future,” Lambert continued.
Josiah Shuman, a junior studying Materials Science and Engineering at Carnegie Mellon University, brought nine fellow engineering students to the event; eight are members of a group he founded, called The CMU Forge Club. Shuman and his friends started with an interest in learning how to create sword and knife blades, and Josiah has been to the Carrie Blast Furnaces for blacksmithing workshops. But, he pointed out, he and his colleagues are more steeped in metallurgical theory, as well as research in such technologies as electronic high-density storage materials and capacitors. Most of them had never witnessed this centuries-old technology—a glowing mass of molten iron smelted and poured.
“It was truly awesome,” said Shuman, “and when it sparked, the staff yelled ‘Turtle!’ and you hunch up your shoulders and tuck your face mask in to protect yourself.”
“Everyone working with the students was so organized and enthusiastic and so helpful,” Shuman continued. “Engineers, and I guess a lot of artists, are really kinda shy and not really outgoing types, but as soon as you make connections, you go out of your way to talk to others at this event, which was a little out of our comfort zone. But I think we’ll maintain a lot of these relationships in the future.”
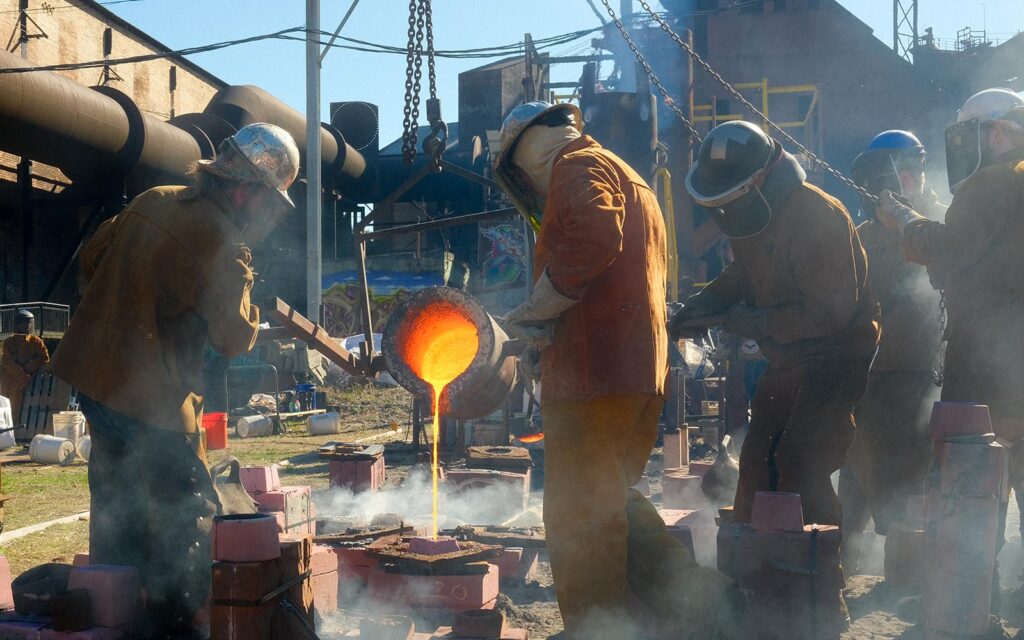
The crew pours iron from the primary ladle.
Building a community in the metal arts is the Pour’s primary objective. Chris McGinnis, Rivers of Steel’s director of arts, explains the inspiration behind this new event: “Rivers of Steel is part of a small but fierce community of people who are passionate about metal casting. And we want to grow that community to more people outside of that fray, to get students excited about metal and the trades and handwork, and share the history of Carrie that they may not know about.”
Carrie provides a truly unique experience for students of metal arts, where 300 to 500 pounds of iron can be melted and poured. The portable furnace used for the event is a scale version of the two giant early twentieth-century blast furnaces that dominate the site, providing a setting unlike any commercial or university campus foundry.
Rivers of Steel has hosted public pours at Carrie, including at the Festival of Combustion and an Iron Casting Spectator Event, but this is the first program focused specifically for university-level students to give them a sense of the history of iron-making in this region and to keep interest and these time-honored technical skills alive.
The scaled-down furnace at this pour is named “Bumblepig” and was designed and built by two of Coral Lambert’s past students, Paige Henry and Kay Dartt. While both are artists, Henry is now Rivers of Steel’s metal arts technician, and Dartt is a professor of art at Shepherd University. Ed Parrish, the metal arts coordinator for Rivers of Steel, who organized and supervised this event, elaborates: “Her full name is Frannie van Bumblepig [local blast furnaces were traditionally named after women from prominent mill families], and she’s an intermittent cupola-style furnace, which means we plug a tap hole with clay, and when the well is full of molten metal, you tap out 300 pounds. We poured a total of about 3,000 pounds of iron at this event.”
The iron is all recycled scrap from such things as old bathtubs, brake rotors, or radiators, combined with limestone and coking coal, heated by propane and then forced air. It duplicates, in scale, the same process that the Carrie Furnaces employed from 1907 through 1978, with the exception that hematite and taconite (iron ore pellets) were used rather than scrap iron.
Experienced artists and those seeing iron poured for the first time all got an up-close, hands-on experience, whether suiting up and actually poking the tap hole and ladling the 2,500-degree liquid iron, or standing by with essential tools.
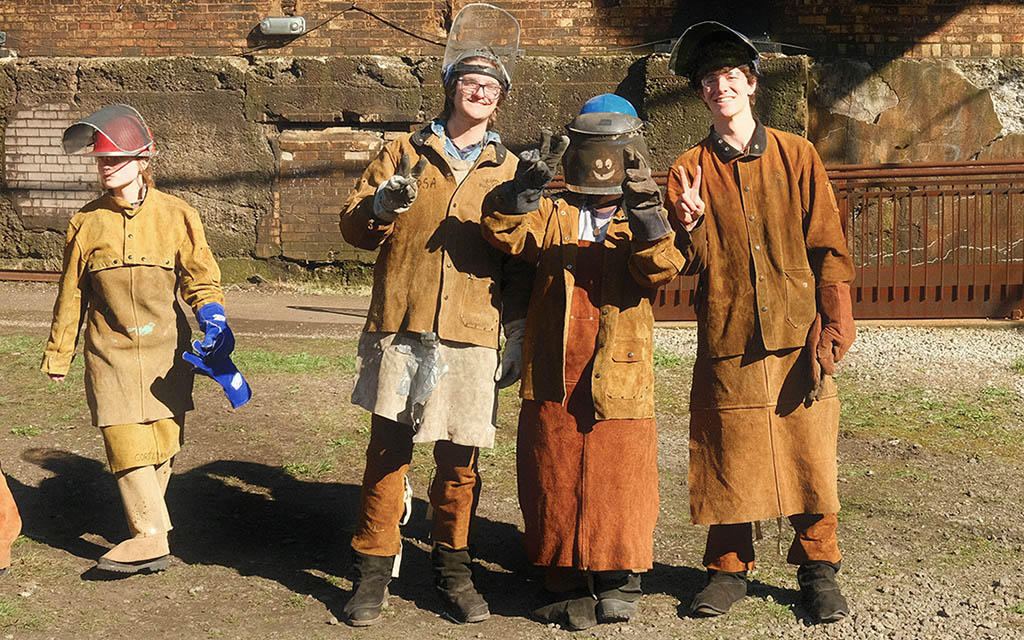
Students prepared to participate in the pour.
“All those who wanted to were given a chance to pour,” Parrish said. “It’s hard work, and it’s a team process. Very orchestrated and controlled. But everyone is generally in awe because it’s very dramatic; there’s a natural theater to this process.” The molten iron was poured into resin, sand-packed molds that many of the students premade and brought with them.
Along with the spectacular visual elements, there was the steady hum of people communicating during the intricate process, the clang of pulley chains as the ladle was hoisted, the hiss of sparks, and the bang-bang as cooled metal was knocked off the poke-hole lance. It was all a faint reminder of the heat, glowing skies, and steady noise that emanated from the massive furnaces #6 and #7 at Carrie, along with up to 1,250 tons of iron daily that each of those two produced in their heyday . . . the entire site produced up to 9,000 tons a day!
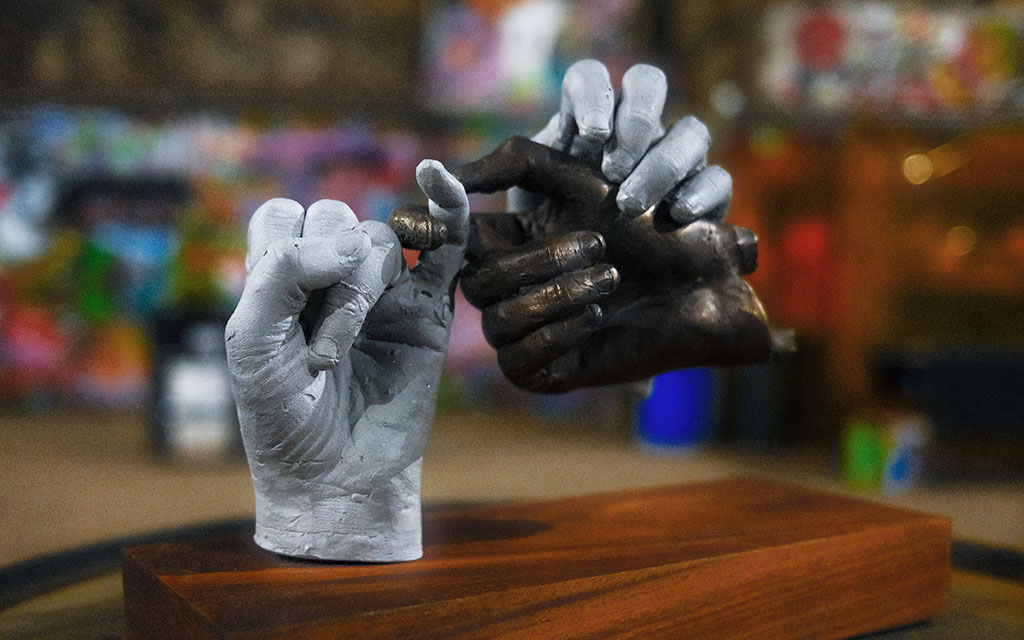
Stay, 2023, aluminum and bronze, by Clark Clark of Shepherd University.
In addition to the big pour on Saturday, students also participated in a pop-up suitcase exhibition on Friday, where they shared “suitcase-sized” works they had created at their schools or studios. Displayed on 55-gallon drum pedestals inside the AC Power House on the grounds of the Carrie Blast Furnaces, there were a variety of cast metal pieces, sculptures, and even a work in neon.
Participants also had a chance to make their own Doodle Bowl, a popular workshop offered at Carrie where molten metal is poured into small molds that can be custom designed by carving out shapes and patterns in a preformed resin bowl. For this premier student event, the bowls were cast in iron, rather than the usual aluminum used during The Doodle Bowl Experience, the publicly offered version of the workshop.
Josiah Shuman and his fellow CMU students cast preformed 4×4-inch tiles as well as the Doodle Bowls. “As engineers, we were laughing, like, ‘We have to get creative now!’ But it was a great chance to explore our artistic side that engineering doesn’t always allow.”
Ed Parrish adds, “Teaching creativity no matter what your field is can be one of the most important things in your toolbox. There’s always a give-and-take with the students, too. I learn as much from them as they do from me.”
Participants were also given a tour of the Carrie grounds and part of furnace #6. Shuman, who had been to a Rivers of Steel’s Blacksmithing Basics: Hooks and Hairpins program in the past, gained even more insight from this event: “Before this weekend, I knew little of iron and steelmaking in Pittsburgh. [On the tour], you could imagine yourself as one of these iron makers decades ago all day, every day, year after year, pouring heaps of hot metal. You feel small next to those furnaces.”
Chris McGinnis, left, led the students through the historic furnaces. Here, they posed for a photo on the stove deck.On Sunday, once the molten iron had sufficiently cooled overnight, Rivers of Steel’s metal arts staff and crew broke the students’ cast pieces out of their molds. The works ranged from very intricate, lacy designs to solid mountain-like forms. “They came out perfect,” said Coral Lambert, who helped with this final stage.
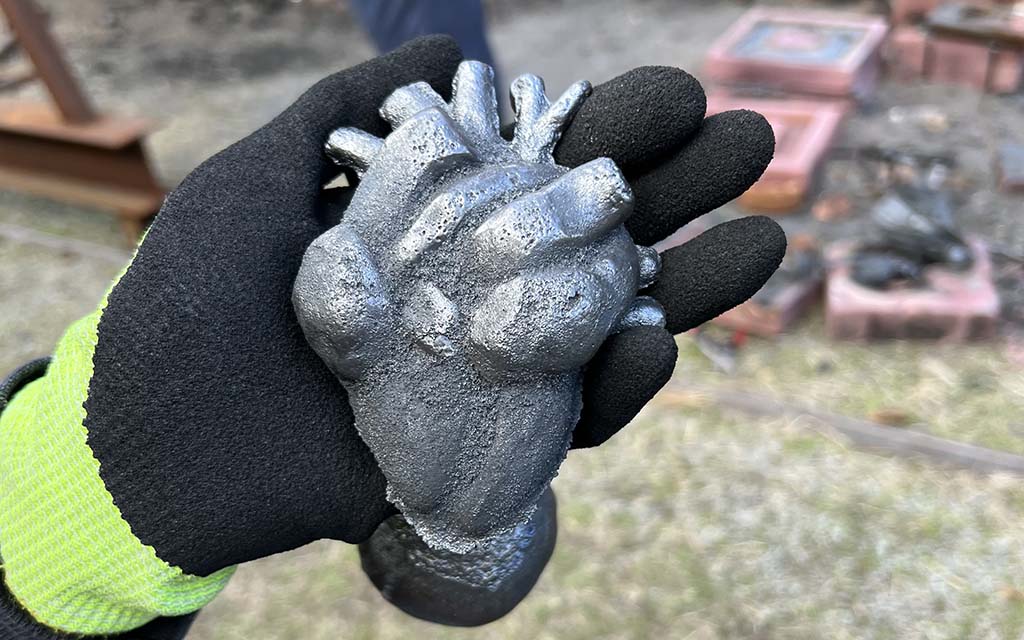
An anatomical heart was one of the items cast.
For mentors like Lambert, the Intercollegiate Iron Pour goes well beyond academics and what can be learned in a classroom. “This is just a melting pot of information that you can be part of and can help shape it for the future. It’s not just the technical stuff, but the important interactions and relationships created.”
Students like Josiah Shuman hope to return to Carrie to work again with staff and other artists. “I’d love to do more of these pours and see what other collaborations—like even a bladesmithing workshop—could come out of it.”
“The connections sparked at this event will serve these artists and engineers well as they complete their schooling and pursue their careers,” said Chris McGinnis. “We hope to see them all again soon!”
Lynne Squilla is a skilled and creative storyteller. She honed her craft as a writer and producer / director of original scripts, documentaries, articles, web content, stage, and other live presentations. While her work has taken her across the globe, she’s rooted in the Mt. Washington neighborhood of Pittsburgh, and has a passion for sharing stories about our region’s past.
Check out the metal arts programs offered by Rivers of Steel.