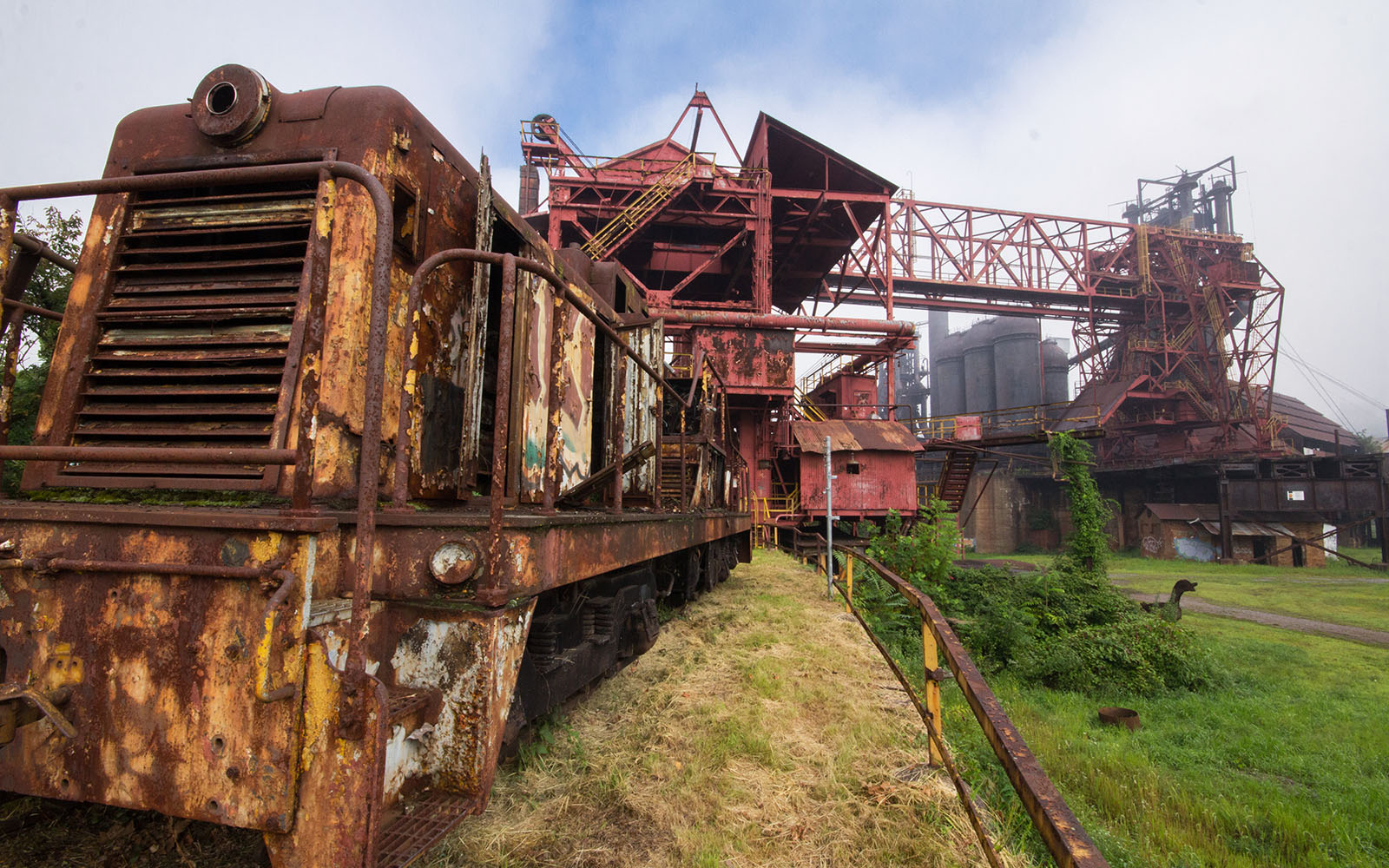
By Keith Clouse, Rivers of Steel Volunteer
Preservation Work on the #101 Locomotive
A large part of iron making is providing the raw materials to the blast furnaces in a timely manner. The logistics require delivery and storage of those materials to allow an uninterrupted supply. The Carrie Blast Furnaces depended upon rail delivery of those raw materials even though it was located beside the Monongahela River. Incoming materials were delivered by three railroads: the Baltimore and Ohio, the Pittsburgh and Lake Erie, and the Union RR. Once inside the Carrie facility it was the job of the Materials Department to unload the freight cars and store the iron ore, limestone, coke, and other ingredients needed for the iron-making process.
Carrie used a huge elevator, called a car dumper, to quickly unload each railcar for distribution into one of three separate storage areas, called ore yards. A General Electric 80 Ton locomotive, #101, would proceed to the arrival yard to pick up three loaded cars. They would be pulled up a ramp to the car dumper. Those cars would be lifted by an elevator and turned over, allowing the contents to fall into a large hopper. After those three cars were emptied, #101 would return to the yard for another group.
For most of its time at Carrie, #101 would run back and forth on a quarter mile of track, rarely venturing from the car dumper. Maintenance and servicing were performed in a small service pit on site. #101 was just one of many diesel locomotives used by the US Steel Homestead Works. However, it had a distinctive cab that made it unique. It was a half cab, the result of an industrial accident at the car dumper. Four large steel arms, controlled by heavy steel cables, held the loaded freight cars in place while the elevator lifted them. One of those cables broke while #101 was underneath it, allowing the huge arm to crash down on the locomotive cab, crushing one side. The operator inside was not injured but was later nicknamed “brown pants” by the rest of the crew.
The car dumper and #101 worked right up to the closing of Carrie in the early 1980s, stored as serviceable for a reopening that never came. Over the years, Mother Nature took over the site, hiding #101 in a small forest of trees and shrubs, entangling the car dumper in vines. As with any machinery sitting in the open, the neglect resulted in rust and vandalism. Even though it was in a fenced in area, #101 was soon covered with an assortment of graffiti, the windows smashed out. It would remain like that, rusted and ignored, until the fall of 2019.
Kevin Scanlon and I began volunteering at Carrie in 2010; we both believed in historical preservation. Carrie was the ideal site for restoration, an example of the iron-making process. Recognizing this, Rivers of Steel was able to National Historical Landmark status for the site in 2006. Kevin and I were among the volunteers working to undo almost 30 years of neglect to open the site for visitors. Early on we worked around the car dumper, cutting away the thick foliage, uncovering the 101. Although the idea of restoring her was something we considered, it would have to wait until more pressing work was completed.
In the fall of 2019, Ron Baraff and Ryan Henderson convinced us it was time to move ahead to begin the restoration of #101. First, we needed a thorough cleaning of the accumulated debris and leaves; taconite pellets were everywhere inside. Next the big job—remove the rust. The first attempt at sand blasting didn’t work out well. It was going to take more time, but using grinders with abrasive disks proved to be a better choice.
It was interesting to work through the layers of paint, discovering three different paint schemes used by US Steel over the years. We worked our way down to bare metal. The body was in good shape for the most part. The were some rust and holes around the sand boxes. The sand had accumulated moisture and rotted through the outside sheeting. Those areas will be covered with sheet metal patches and the missing roof hatch covers will be replaced at the same time. Because bare metal will quickly rust, Rivers of Steel provided primer to cover it. Each section was painted as the rust was removed. When the painting was completed, we stood back to admire the now renamed “Miss Carrie” in her new red dress.
So far, the work had stabilized the locomotive, but winter was fast approaching. We needed to replace the broken glass to prevent further damage to the interior of the cab. A large sheet of Lexan was cut into the appropriate shapes to replace the glass. The floorboards were warped and broken, so a temporary plywood floor was installed and braced. A decision was made to use the 1960s paint scheme—blue with orange stripes. It was decided that we would wait until spring before attempting to do the finish work. We had taken the dimensions and made sketches of the safety striping while removing the old paint. That will be our guide when we are able to add the final touches.
We are currently in a holding pattern until the virus restrictions are lifted. Even at this point, the project has been very satisfying. We were able to restore and preserve a unique part of the Carrie iron-making process. So far, the only negative was feedback from people who liked the former rusty look for photos…I can live with their disappointment.
Guide to Images
Featured Image: An unrestored Carrie #101 locomotive with the car dumper, ore bridge, and the Carrie Blast Furnaces in the background
Image 1: Tour Guide Keith Clouse
Image 2: Kevin Scanlon grinds away the rust
Image 3: Before and after images of the first phase of the “Miss Carrie” restoration